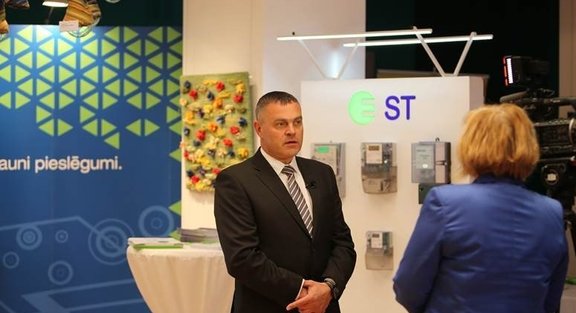
"Так как в Латвии очень велик удельный вес воздушных электролиний, собственное производство деревянных опор - лучшее и экономически наиболее выгодное решение для обеспечения основной деятельности всего предприятия. Мы традиционно используем для строительства и содержания электролиний низкого и среднего напряжения деревянные опоры, произведенные предприятием. Именно деревянные опоры признаны в качестве безопасных и экономически выгодных в нескольких странах Скандинавии, а также в Латвии, к тому же, при точном соблюдении технологии обработки - также дружественными среде", - отмечает член правления AS "Sadales tīkls" Сигнис Ринс.
Исторически специфика электросети в Латвии - в ее обширности и раздробленности, 70% составляют воздушные линии. Их протяженность в Латвии достигает 66 тыс. км, воздушные электролинии пересекают покрытые лесом территории (около 21 тысяч км), сельскохозяйственные земли и населенные пункты. Всего в воздушных линиях используется свыше 1,6 миллионов опор, т.е. почти по одной на каждого жителя Латвии", - такое сравнение упоминает С. Ринс.
Производство деревянных опор находится в местечке Бранкас Озолниекского края с 1971 года и занимает площадь в 8 гектаров. Это одно из крупнейших производств деревянных опор в странах Балтии, к тому же есть еще только нескольких заводов, где можно производить деревянные столбы длиною от 10 до 16 метров. В основном из выращенной в латвийских лесах сосны в Бранкас изготавливают деревянные опоры для электролиний низкого напряжения - 0,4 кВ и среднего напряжения - 20 кВ, ежегодно производится до 50 тыс. таких столбов.
По оценке С.Ринса, прошлый год был для завода по производству деревянных опор очень успешным. "Достигнув поставленной в прошлом году цели, предприятие смогло произвести рекордное количество деревянных опор - 46 тысяч. Было начата реализация утвержденного предприятием плана развития, направленного на повышение объемов производства и эффективности, снижение себестоимости произведенной продукции. Расширены также существующие сушильные площадки, закуплена новая, современная техника. Проведя исследовательские работы, мы поняли, что можем производить высококачественные, отвечающие техническим требованиям опоры, если сравнивать с опорами, закупаемыми у других поставщиков, которые часто не выполняют этих требований", - поясняет С.Ринс.
Главные задачи завода - это приемка древесины для опор, контроль ее качества, очистка от коры и сглаживание. Затем следует сушка и, наконец, импрегнирование древесины. Так как относительная влажность свежеспиленной древесины обычно превышает 60%, то для ее атмосферной сушки необходимы большие площади и время - от 6 до 8 месяцев. Заботясь об окружающей среде, на предприятии по производству опор регулярно проводится мониторинг грунта сушильных площадок и профилактические мероприятия по защите среды.
В Латвии на воздушных линиях электропередач используются деревянные столбы, прошедшие химическую обработку, срок службы которых - не менее 30 лет. Для производства столбов используется только древесина сосны (Pinus Silvestrus), выросшей в странах Балтии. Заболонная часть сосны благодаря своей структуре хорошо подходит для эффективного использования консервантов древесины. После очистки от коры, сглаживания и сушки древесину в автоклаве пропитывают антисептиками, после чего ее можно использовать для закапывания в грунт в прямом контакте с почвой.
В настоящее время на предприятии деревянные опоры сушат атмосферным способом, складывая их в штабеля, в которых они сохнут 6-8 месяцев. "Если климатические условия неблагоприятны, то столбы не сохнут, и это может вызвать непредвиденные отклонения в успешном выполнении плана по производству опор. В таких случаях, чтобы не задерживать строительство объектов электроснабжения, мы закупали деревянные опоры у внешних поставщиков, однако качество импрегнирования, или пропитки, у таких закупленных готовых опор не отвечает критериям, установленным предприятием", - поясняет С. Ринс, добавляя, что это основной аргумент в пользу решения о модернизации производства деревянных опор.
"Чтобы повысить качество процесса производства опор для электролиний, в рамках модернизации мы планируем заменить отработавшее свой срок обрабатывающее оборудование, а также думаем о способах уменьшения влияния производственных процессов на окружающую среду. Шагом навстречу зеленому мышлению стала замена использовавшегося ранее химического консерванта, содержащего хром и мышьяк, на более дружественный среде органический с содержанием меди", - поясняет С. Ринс.
В последние годы AS "Sadales tīkls" осуществило значительные инвестиции в развитие производства опор. В процессе погрузки и транспортировки древесины очень успешно применяются два самоходных погрузчика "Sennebogen" и фронтальный погрузчик "Doosan". Эта современная техника позволяет повысить производительность и безопасность труда, уменьшить количество технологических процессов, а также использование рабочей силы.
Планируется, что в этом году вместо старого, изношенного оборудования по очистке от кожуры и сглаживанию древесины начнут работать новые машины немецкого и финского производства, а для более быстрой сушки древесины строятся две новые сушильные камеры - сушилки для древесины. Кроме того, предусмотрено построить новую, современную котельную, где можно будет полностью использовать отходы, возникшие в процессе очистки от коры и сглаживания древесины с высокой содержанием влаги, тем самым обеспечивая полностью безотходный процесс производства.
"В этом году должна быть завершена реализация плана развития производства деревянных опор - установлены запущены новые линии по очистке от коры и сглаживания древесины, построена новая котельная. В результате мы сможем подготавливать до 40% необходимой ежегодно древесины независимо от погодных условий и стоимости энергоресурсов, достигнув цикличности производства. Реализации проекта позволит в будущем уменьшить запасы древесины на площадках, повысить эффективность производства, а также уменьшить себестоимость произведенной продукции", - намечает основные цели и задачи С.Ринс.